Understanding The Role Of IoT In Streamlining Battery Production

By Emily Newton
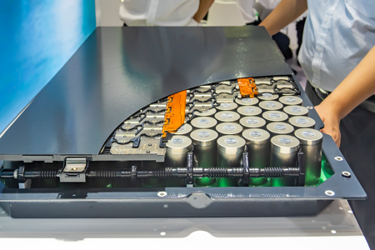
Lithium batteries are among the most crucial components in modern electronics. As the Internet of Things (IoT) grows and electric vehicles (EVs) become more common, battery demand is surging. Meeting the rising pressure for production speed and quality can be challenging, but new technologies hold an answer.
While the IoT is itself a key driver of battery demand, it plays a critical role in the manufacturing of these devices. Understanding its potential in this area is the first step in optimizing workflows to meet the growing need for reliable, widely available lithium-ion batteries.
Sourcing Transparency
The IoT’s role in battery production starts before manufacturing even begins. Real-time monitoring solutions throughout the supply chain provide transparency to mitigate delays and avoid regulatory complications in an organization’s sourcing practices.
Supply chain delays are common. Beyond that, many battery materials carry ethical and environmental concerns. Roughly 70% of the world’s cobalt comes from areas where unsafe work practices and child labor are common. Manufacturers must address both issues to remain efficient and compliant, but this requires deeper insight into their sources.
IoT tracking systems can reveal precisely where each shipment comes from, making it easier to ensure ethical sourcing. Such devices also provide real-time location updates. Battery manufacturers can use this information to predict and respond to incoming delays to minimize their ripple effects and maintain productivity.
Digital Twins
Once materials reach production centers, facilities can use the IoT to generate digital twins of their workflows. These virtual models update as new information comes through smart devices, providing detailed simulations of a manufacturer’s operations.
An estimated 70% of manufacturers today already use these technologies to evaluate their processes. In the context of lithium battery production, this may look like analyzing workflows for bottlenecks or common sources of errors. After recognizing these flaws, businesses can simulate changes in their digital twins to estimate how well such adaptations address them.
The simulations remove the guesswork from optimization. In turn, battery production facilities can boost throughput and minimize waste without disruptive trial and error. Faster process improvements also make it easier for manufacturers to scale to meet growing demands.
Quality Assurance
Today’s batteries must meet extreme expectations. Lithium titanate-oxide batteries, for example, can maintain 80% capacity after 25,000 charging cycles, but such standards are not easy to achieve. These metrics leave little room for error, so reliable quality assurance is essential.
IoT devices can monitor factors like voltage, operating temperatures, and current in testing to provide detailed information on product performance. Others can track batteries and their environment as they move throughout the production line to ensure conditions remain optimal. Once anything falls below benchmarks, IoT systems alert manufacturers to the issue.
Using the IoT to perform such analysis gives enterprises more hard data while minimizing the time it takes to collect it. As a result, they can avoid costly errors without increasing lead times.
Predictive Maintenance
Maintaining peak productivity also requires attention to a facility’s equipment health. Manufacturers lose 800 hours per year to machine downtime, but much of this unproductive time is preventable. The IoT can help by enabling predictive maintenance.
Predictive maintenance uses IoT sensors to monitor equipment performance indicators in real time. As soon as any metrics suggest the machine will need repairs, the system alerts key stakeholders. Consequently, technicians can schedule a time to fix the machinery before larger breakdowns occur, minimizing unplanned downtime.
This practice also reduces planned downtime because all repairs are needs-based, not time-based. Manufacturers using preventive maintenance eliminate unnecessary repairs and inspections without increasing their risk of a malfunction. While such systems can be expensive and challenging to implement, the resulting savings and impact on throughput are worth it, especially in the growing battery sector.
Shipment Security
IoT solutions continue to bring value to battery manufacturing after production. While lithium titanate-oxide batteries are more resilient than their conventional counterparts, similar products can still incur damage during shipping. Greater visibility into downstream supply chains helps brands prevent such incidents.
The same tracking systems providing real-time updates on incoming shipments can offer assurance in outgoing ones. IoT sensors can monitor humidity and heat inside battery packages to ensure conditions remain ideal. That way, logistics providers can react when things go awry, such as dropping packages off at a closer location amid high temperatures to prevent damage.
Many lithium batteries contain a flammable electrolyte, introducing combustion concerns if physical damage occurs. Consequently, ensuring safe shipments is crucial to the electronics industry. Tracking these packages in real time will protect logistics employees and minimize product loss in transit to boost overall efficiency.
Future Areas Of Opportunity
Battery manufacturers can use the IoT to drive longer-term optimizations, too. Tracking a product’s performance in its end use reveals helpful information about where future iterations can improve. The IoT provides the necessary insight for these upgrades.
Studies have found IoT battery-monitoring technologies can optimize energy storage and distribution for renewable electricity infrastructure. Over time, these devices would reveal trends in how the storage solution performs, including commonalities in situations where it’s failed. Manufacturers can use these insights to redesign their batteries to address similar issues in the future.
Ongoing insights like these are most impactful in emerging markets, such as EVs or medical wearables. Collecting user data through the IoT could let companies generate digital twins of their battery products to streamline the redesign process. As a result, the industry would adapt to meet shifting demands with less time and investment.
The IoT Takes Lithium Batteries To New Heights
Lithium titanate-oxide batteries and similar novel energy storage technologies are becoming increasingly crucial amid rising tech adoption. The electronics manufacturing sector must adapt to ensure it can meet these needs now and in the future as it grows. Capitalizing on the IoT is a vital step in that adjustment.
IoT connectivity provides the insight and control organizations need to make batteries faster, with fewer errors, and more safely. These benefits can come from applying smart devices in any part of the supply chain, too. As more of the sector recognizes this potential, lithium-ion batteries will deliver more value.