Integrating Advanced Polymers: Why It Matters For Your High-Power RF Design

By Emily Newton
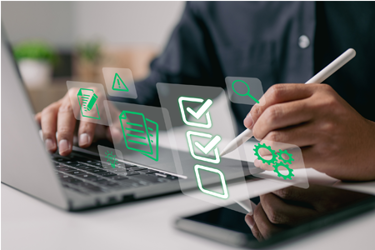
Insulating polymers play a critical role in wireless electronics design. High-powered RF components, in particular, must take material selection seriously to strike an optimal balance between temperature, signal, physical strength, and circuit efficacy. New thermal management polymers make these complex decisions easier.
Electronics engineers have far more than simple silicone at their fingertips today. Still, advanced polymers introduce new cost and production considerations, so some professionals may hesitate to embrace them. Despite those fears, integrating these materials is crucial for several reasons.
Thermal Management
Novel polymers’ thermal management is among their most impactful benefits. Overheating is the most common cause of failure for electrical components, but today’s miniaturization trend often leaves little to no room for active cooling systems. At the same time, some insulators must retain heat to ensure battery performance in cold outdoor environments.
Composite phase-change materials (PCMs) are some of the most promising polymers in this arena. As PCMs shift between varying levels of solidity, they absorb, transfer, or release thermal energy across the area. Consequently, they provide a compact, passive way to prevent overheating on high-power components while insulating those that suffer performance loss in colder temperatures.
Integrating nanomaterials like graphene into a polymer provides similar benefits. Microscopic structures can efficiently divert excess heat to new areas without bulky heatsinks or fans. Achieving the same efficiency with conventional alternatives would require far more space and complex components.
Electrical Insulation And Conductivity
Similarly, advanced materials provide better electrical insulation. Like thermal management polymers, these insulators must work both ways. Circuits should be able to transmit signals quickly, but such transfers cannot reach a point where they interfere with other components or device safety.
Boosting electrical conductivity while reducing thermal conduction is difficult with conventional resources. High-powered RF applications further complicate it by raising the need for strong electrical signals while introducing heightened temperature concerns.
One solution is to use thermoelectric materials to convert what would otherwise be waste heat into an electrical signal to supplement power sources. Engineers also can add nanostructures to hydrogels to capitalize on their conductivity while reducing thermal sensitivity.
Physical Protection
High-power RF device materials must also take physical safety into account. In today’s market, many such electronics are Internet of Things endpoints and, as such, have to withstand rigorous environments.
Thermal management is part of this protection, but insulators should provide some amount of shock absorption, too. Conventional options like silicone are often too soft to safeguard sensitive components without additional structures, which take up space. Newer alternatives can boost physical defenses without sacrificing room or thermal conductivity.
Nanomaterials can add strength despite being 10,000 times smaller than human hair, making them an ideal choice. Alternatively, some PCMs can harden against physical shocks to protect sensitive parts while remaining light to facilitate better thermal conductivity at other times.
Maintaining Signal Integrity
As an additional challenge, insulating polymers must provide all the above benefits without interfering with a strong wireless signal. That means letting desired RF waves through and stopping unwanted RF radiation to minimize electromagnetic interference (EMI).
Conventional EMI shields use metals, which are unsuitable for compact applications where temperatures and electric signals are also a concern. Filling polymers with conductive elements enables a best-of-both-worlds approach. Hybrids can achieve EMI shielding efficiency of up to 130 decibels while maintaining polymers’ thermal management benefits.
Conductive and magnetic polymers provide similar advantages. Across all material types, these novel resources are preferable to older alternatives because they maintain both signal integrity and thermal and electrical management in a single solution. As devices get smaller, that functionality will only become more important.
Keys To Integrating Advanced Polymers
Demands for high-power RF systems are rising. Electronics designers must capitalize on advanced polymers to keep up, but these materials also have unique implementation concerns. Consequently, engineers should pay attention to a few optimization opportunities.
Determine The Ideal Polymer
Making the most of next-generation polymers starts with choosing the ideal composite. That decision can be difficult because the best material depends on the specific device in question.
Polymers with carbon nanotube fillers are ideal for strength and thermal management but don’t offer as much EMI shielding as some alternatives. Hydrogels are great for electrical conductivity but require additional materials for physical protection and heat resistance. Businesses will likely have to sacrifice in one area, so they should start by identifying which factors are most important for their use case.
Costs and material availability should play a role in this decision-making, too. Graphene has potential in virtually every aspect of high-power RF design but often costs between $67,000 and $200,000 per ton, making it inaccessible to most organizations.
Optimize Production Processes
Electronics manufacturers may also need to adopt new production methods to work with novel resources. Consequently, it’s crucial to review any unique workability constraints of a polymer before choosing one.
Many next-gen materials are costlier than conventional alternatives, so engineers should also consider cost-saving workflow changes. Roll-to-roll die cutting can be advantageous for soft, tacky polymers, increasing yields by as much as 30% and reducing waste. Other possible process improvements include automated quality control and 3D printing.
Capitalize On AI And Automation
Across all production processes and polymers, manufacturers should automate as much as possible. Manual work is inherently error-prone, leading to material waste. While that may not be a huge issue with conventional insulators, it quickly becomes expensive with advanced polymers.
Automated solutions like robotic machining arms and 3D printing can lay down next-gen thermal management polymers in less time with less waste. As a result, such resources become more cost-effective to implement.
Similarly, artificial intelligence can yield impressive results in the design phase when adjusting products to integrate these materials. Some models have designed chip components to be 5% smaller and take just 10 days to optimize plans instead of months. Improvements like these can dramatically improve production costs while making advanced polymers easier to use.
Thermal Management Polymers Are Evolving
As demands rise, thermal management polymers must become more versatile. Achieving today’s standards of temperature control, electrical conductivity, physical protection, and signal strength is only possible with advanced materials.
No composite is perfect, but next-generation polymers unlock new possibilities. The sooner companies learn to take advantage of these opportunities, the better they can serve the markets of tomorrow.