The Relationship Between Aerospace And Electromagnetic Simulation

By John Oncea, Editor
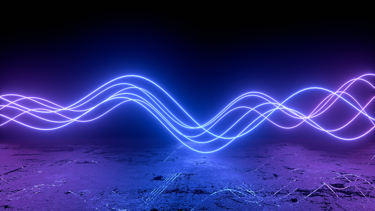
Electromagnetic (EM) systems come with their own set of challenges, such as very wide frequency ranges and electrically large structures with very fine detail. EM simulation can help engineers overcome those challenges by allowing them to investigate the electromagnetic properties of components or whole systems efficiently.
EM simulation can be applied throughout the entire design process, from an idea’s inception to final production, to meeting specifications, to analyzing the electromagnetic performance under operational conditions. In short, EM simulations are transforming the design cycle. The benefits EM simulation provides range from reducing the time and cost of bringing a product to market to improving analysis from antennas, sensors, and chips up to entire devices, including aircraft, smartphones, and MRI.
Multiple industries are benefiting from EM including high-tech industries such as electronics and communication. But other industries – defense, transportation, and life sciences – are benefiting as well. Let’s take a look at aerospace, another of the industries reaping rewards from EM simulation.
According to this Siemens webinar, to maneuver effectively and successfully carry out missions spacecraft are equipped with electrical and electronic devices so critical that any malfunctions or disruption must be avoided at all costs. The disparate types of electronic equipment within a satellite – including surveillance and communication equipment – must be mutually compatible. They also must be compatible with any outside source of electromagnetics interferences, including electrostatic discharge.
“During the design phase of space systems, it is crucial to apply electromagnetic simulation to understand and reduce risks related to electromagnetic compatibility (EMC),” writes Siemens. “Emission and susceptibility, both radiated and conducted, are key qualifiers in the context of EMC, as well as electromagnetic interferences (EMI) between the antenna systems of the satellite.”
One specific area in aerospace design benefitting from this approach, as reported by Digital Engineering 24/7, is electromechanical systems simulation. “As our products have become more and more complex, the systems on the aircraft have become electromechanical systems,” says Dale Tutt, vice president of industry strategy at Siemens Digital Industries Software. “In the past, we thought of them as mechanical systems or electrical systems.
“Today, however, everything is a mechatronic system that has mechanical, electrical, electronic, and software elements. As a result, we are now designing multidomain systems, so the design and simulation tools have had to mature with those as well. Advanced simulation and data management systems are no longer optional.”
Guillermo Leturio Barea, business development executive at SimScale, adds, “Simulation will play a major role in de-risking this transition and the evolution of the aircraft powerplant. Similar to structural and fluid simulation tools, electromagnetics simulation tools also have evolved. These include improvements in ease of use, solver speed, and solver ability to use high-performance computing. Workflows also have been progressively simplified, with very intuitive template- and table-driven tools evolving rapidly in the past five years.”
Digital Engineering 24/7 notes the adoption and implementation of EM simulation systems can be challenging, including the creation of the mechanisms and infrastructure required to feed simulation data into their digital threads. By doing this, aerospace companies can understand more efficiently what-if scenarios such as when they are considering changes in suppliers, material grades, or machining process tolerances.
“The inclusion of simulation data is also important because aerospace companies must understand in real time the performance and wear and tear on complex, expensive, and safety-critical assemblies like aircraft engines and airframes,” writes Digital Engineering 24/7.
“The chief challenge is the sheer quantity of simulation data that must be managed, quantified, and analyzed to make the product life cycle as efficient as possible,” says Philip Kinnane, senior vice president of sales at COMSOL. “Reducing the amount of unnecessary or less important data or ideas that will never lead to fruition, at the level of the creation of simulation data — the modeling and model — permeates through the workflow of the digital thread and leads to better results, faster.”