6 Surprising Facts About Wire

By John Oncea, Editor
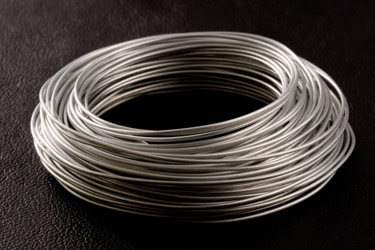
RF wire tech is rapidly evolving, enabling 5G/6G, defense, and smart monitoring, with miniaturization, durability, and sustainability driving innovation.
In my job, not every story can be about neutralizing drone swarms with radio waves, understanding satellite orbits, or NASA acquiring GPS signals from the moon. No, sometimes I have to cover amplifiers and oscillators, power electronics, and interconnects. You know, not flashy topics, but the active and passive components that keep the RF industry humming. Kind of like today’s topic: wire.
On the surface, there doesn’t seem to be much there when it comes to wire. Still, as Everything Everywhere Daily writes, “The modern world runs on metal wires. These thin metal strands literally circle the globe and are responsible for much of the world’s electrical power and communications. It is something so basic that most people never bother to stop and think about how wires are made.”
So, let’s dig into how wire is made, as well as the history and some other facts you may not know about this 2,000-year-old invention.
A Brief History Of Wire
Wire, a seemingly simple product, has played a crucial role in shaping technology, industry, and society for thousands of years. Its history is a story of continuous innovation, from ancient handcrafting to the highly mechanized and precise processes of today.
“It turns out wire has been made for thousands of years, although its uses have changed dramatically,” writes Everything Everywhere Daily. “The earliest evidence of wire dates back to around 2000 BCE in ancient Mesopotamia and Egypt. These early wires were typically made of precious metals such as gold and silver, hammered into thin strips, and then rolled or twisted by hand into filaments. These wires were primarily used in jewelry, decoration, and ceremonial objects. The softness and malleability of these metals allowed artisans to work them without needing advanced tools.”
The technique used by these early craftsmen was drawing by hand. This involved pulling a metal rod or strip through a tapered hole in a hard material, such as stone, to produce thinner strands. This basic method – pulling metal through a hole smaller than itself – remains at the heart of wire production even now.
As the wire is drawn through progressively smaller holes, it becomes thinner and longer, with its volume remaining constant. Early wires were typically made of copper and bronze and used for decorative metalwork, jewelry, and woven patterns, especially in the Mediterranean and South Asia, according to Southwest Wire Rope.
During the Greco-Roman period, wire-making advanced significantly. The Romans developed drawplates-tools with holes of diminishing sizes-to create wires from iron, bronze, gold, and silver. These wires were used in brooches, chains, musical instruments, and even some structural applications. However, production remained artisanal, and the quality and uniformity of wire varied greatly.
The Middle Ages saw further advancements, particularly in the Islamic world and later in Europe. Islamic craftsmen refined metalworking techniques and began using drawplates for harder metals like steel. In India and the Middle East, artisans developed sophisticated methods for drawing fine gold and silver wire, especially for textile embellishment.
By the 13th and 14th centuries, wire production in Europe expanded, with Nuremberg, Germany, becoming a major center. The introduction of water-powered wire-drawing mills in the late Middle Ages mechanized the process, improving both speed and consistency.
From Chainmail Armor To Barbed Wire
One of the most important uses for wire throughout history was in the manufacture of chainmail armor. Believed to have originated with the Celts around the 4th to 3rd century BCE, chainmail required consistent, durable, and flexible metal rings. Early chainmail was crafted by hammering iron or bronze into thin rods, then cutting and shaping them into rings, which were riveted or butted together in a four-in-one pattern. This innovation not only provided effective protection in battle but also drove advances in wire-making technology.
The Industrial Revolution fundamentally transformed wire manufacturing. In 1773, Samuel Walker introduced the continuous rolling mill, enabling the efficient production of uniform iron rods for wire drawing. The adoption of steam power further revolutionized the industry, allowing for the mass production of wire with unprecedented consistency and at much lower cost. In the 1830s, the first practical steel wire was produced, offering greater strength than iron. According to Britannica, the Bessemer process, introduced in 1856, made the mass production of steel wire economically viable for large-scale applications.
The development of wire rope, or metal cable, was another major milestone. In 1831, Wilhelm Albert in Germany created the first wire rope for mining hoists by twisting several strands of wrought iron wire into a helical pattern. This design proved more resilient and dependable than traditional hemp ropes. American engineer John A. Roebling improved on Albert’s design in the 1840s, creating stronger, more flexible steel wire cables. Roebling’s cables became critical in building suspension bridges, most famously the Brooklyn Bridge.
The 19th century saw wire become essential to modern communication and infrastructure. Samuel Morse’s telegraph system in 1844 relied on copper wire to transmit messages across great distances, and by 1861, the first transcontinental telegraph line connected the United States.
The invention of barbed wire in the 1870s and the telephone in 1876 further increased demand for wire, especially copper, for communication networks and electrical power distribution. Thomas Edison’s first electrical power network in 1882 also depended on copper wire to deliver electricity, marking the beginning of the modern electrical age.
Wire In The Modern Age
In the 20th century, wire manufacturing diversified rapidly. The automotive and aviation industries relied on steel wire for tire reinforcement, springs, and control cables. Wire rope enabled the construction of larger suspension bridges and revolutionized mining and transportation. World Wars I and II accelerated innovation, as high-tensile steel wire became essential for aircraft, military communications, and electrical applications. Manufacturing processes became more standardized, and quality control more rigorous.
After World War II, wire production became increasingly sophisticated. Modern techniques involve hot rolling metal into rods, acid cleaning, and cold drawing through precision dies made of diamond or tungsten carbide. Computer-controlled machinery now ensures tolerances measured in micrometers. By the 1970s, wire manufacturers were producing ultra-fine wires for integrated circuits and microelectronics, with diameters measured in thousandths of a millimeter.
Today, wire is indispensable to nearly every aspect of modern life, from electrical devices and communication systems to transportation and engineering. All of this progress is built on techniques developed thousands of years ago, evolving from the simple act of pulling metal through a small hole.
Surprising Facts About Wire And The RF Industry
Wire is fundamental to the RF industry, but its use goes far beyond basic signal transmission. Recent innovations and applications reveal surprising facts about how wire and cable technology are evolving to meet the demands of innovative RF systems.
One of the most striking trends is the relentless push toward miniaturization, reports Connector Supplier. RF connectors and cables are now being engineered to operate at frequencies well above 145 GHz, a range once considered the exclusive domain of bulky, rigid waveguides. The latest 0.6 mm connectors can function at sub-terahertz (THz) frequencies, enabling new possibilities in 5G, 6G, and advanced IoT applications. This miniaturization is not just about saving space; it allows for automated assembly and integration into densely packed devices, which is critical for the next generation of mobile and wireless technologies.
The RF industry’s use of wire isn’t limited to communications, Tech Briefs writes. Recent breakthroughs have seen coaxial cables and assemblies used in phased array radar systems and even in radio frequency directed energy weapons (RFDEW). These weapons, developed for defense applications, use high-powered RF signals delivered via advanced cable assemblies to disable or destroy electronic components in drones or other threats. This marks a significant evolution from traditional uses, placing wire at the center of electronic warfare and military asset protection.
Modern RF cable assemblies are engineered to withstand extreme conditions, including high temperatures, vibration, and environmental exposure, Orbis Systems writes. In aerospace and military applications, cables must maintain performance under stress and in challenging environments. Flexible coaxial cables are prized for their adaptability in tight spaces, while semi-rigid and high-frequency cables offer unmatched signal integrity for radar, satellite communications, and electronic warfare systems. This focus on durability has led to the adoption of new materials and manufacturing techniques that extend product life and reliability.
Another surprising development is the emergence of “smart” RF connectors and cables. These components are now being integrated with sensors that monitor real-time performance metrics such as temperature, signal degradation, and moisture. This capability allows for predictive maintenance, reducing downtime and preventing failures in mission-critical systems. Such innovations are particularly valuable in sectors like telecommunications, medical imaging, and industrial automation, where reliability and uptime are paramount.
Sustainability is becoming a significant consideration in RF wire and cable manufacturing. Companies are increasingly using recyclable materials, lead-free components, and corrosion-resistant finishes to comply with environmental regulations and to meet customer demands for greener products. Improved sealing and wear-resistant contacts are also being developed to ensure long-term performance, even in harsh environments. These changes reflect a broader industry shift toward responsible manufacturing and life cycle management.
The deployment of 5G networks and the research into 6G are driving demand for advanced RF cable assemblies capable of supporting higher data rates and lower latency, MarketWide Research reports. E-band frequencies (up to 90 GHz) are now being used for backhaul transmission, and there is growing demand for both high-frequency and low passive intermodulation (PIM) cables. The need for phase-stable and low-loss cables is especially acute in applications like wireless base stations, satellite systems, and test setups, where signal integrity is mission-critical.
Wire in the RF industry is no longer just a passive conduit for signals. It is a dynamic, rapidly evolving technology at the forefront of some of the most advanced applications in defense, communications, and beyond. From miniaturized connectors operating at sub-THz frequencies to smart cables that monitor their health, the humble wire is proving to be a surprisingly innovative and indispensable component in the RF landscape.