3 RF EDA Challenges — And How To Solve Them
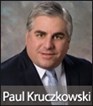
By Paul Kruczkowski, Editor
In my previous career as an RF engineer, I was part of a broadcast engineering design team that used EDA software tools to get our designs into production and ultimately to market faster and with fewer design issues. Even though these software design tools were extremely powerful, they were not without their limitations.
For example, our 3D full-wave EM simulator could accurately model and simulate RF filters, but it lacked a refined system-level environment to effectively manage multiple solvers, including thermal analysis of the filter structure. Our 2D/3D planar tool was also very capable — until we wanted to use multiple substrate topologies in a single circuit. In addition, our EDA tools lacked the ability to interface with test automation software and test equipment in the laboratory, in order to replace simulated data with measured data.
If only I were still an engineer! The next generation of EDA tools is helping today’s engineer overcome these complex design challenges in ways that were not available to my team. Here’s how…
Accounting For Impact Of Thermal Properties On RF Performance
Even after the filter synthesis, 3D modeling, and 3D full-wave simulations (including parametric sweeps) are complete, the thermal properties of the filter are not yet accounted for. Anyone familiar with RF emission filters knows that they are often mechanical in nature, comprised of multiple resonant structures, such as cavities, rods or ceramic pucks, as well as many tuning and coupling adjustments — typically screws, rods, metal loops, or apertures. All of these elements are subject to RF heating and ambient temperature changes, which cause unequal expansion and contraction of these parts, thus affecting the center frequency and shape of the filter’s frequency response. Lacking an elegant way to simulate these phenomena, my team used expensive specialty metals and temperature compensation techniques, and verified the filter’s performance in a thermal chamber.
Today’s RF engineers, however, can manage complex analysis involving multiple solvers to improve the design process, using tools like Computer Simulation Technology’s (CST) System Assembly and Modeling (SAM) environment in CST Studio Suite 2012. SAM enables an engineer to combine the typical 3D electromagnetic analysis of, in this case, the filter with a thermal analysis of its structure. In addition to providing insight into problematic thermal hot spots, SAM specifies the structural changes of the filter related to temperature changes. It also provides new geometry for additional EM simulations to analyze changes in frequency response and response drift due to temperature.
Simulating Circuits With Multiple Topologies
Another challenge my team faced was simulating circuits that utilized more than one substrate topology. A simplified example of this point would be simulating a complete circuit consisting of two amplifier sub-circuits feeding a microstrip Wilkinson power combiner with a stripline directional coupler providing samples to detector circuitry. In such a scenario, the engineer was forced to simulate incompatible sections of the circuit separately, since the board stack of the stripline was incompatible with the stack of the microstrip. The engineer could cascade the simulations for system analysis; however, that approach ignored all interactions that might exist between those subcircuits.
Today, engineers are simulating much more complex circuits than the simple example I provided above, and designing multichip RF modules, complex ICs, and integrated microwave assemblies (IMAs) often involves many different topologies and interconnect levels. In response, EDA software developers are creating new tools to help simplify such complicated designs. Agilent EEsof EDA recently added capabilities to its Advance Design System (ADS) to model and simulate circuits that bridge multiple substrates — and reconcile the multilayer interconnect on a single schematic. This improved schematic functionality, combined with the integrated Momentum 3D planar solver and layout capabilities, gives engineers the ability to simulate complex circuits in their entirety to detect and solve issues before manufacturing and assembly, allowing them to design closer to the margins.
Disconnect Between Design Tools And The Lab
Simulation, analysis, and circuit layout is only the beginning of a new design. The real work starts in design verification in the laboratory, where component tolerances, parasitics, interactions, and layout decisions make the design cycle interesting. At my previous company, we had no elegant way enhance our simulations by introducing measured data, since our EDA software lacked a convenient way to co-simulate with automated testing platforms or to interface with test equipment. We simply left our computers in the office,office; due to this disconnect between the lab environment and our design tools.
Much progress has been made in this area since I left the lab. In fact, EDA software is now as comfortable in the lab as the test and measurement instrumentation they connect to via a GPIB or LAN connection. Since its acquisition by National Instruments (NI) last July, AWR has added refinements to its Microwave Office 2011 software that cohesively integrate Visual System Simulator (VSS) with NI’s LabVIEW. This union combines VSS’s environment for circuit modeling, input signal generation, and result measurement with LabVIEW’s DSP (digital signal processing) functions, signal generation, and toolkits for telecommunication standards as well as RF instrument control and RF measurement. VSS can co-simulate with LabVIEW, with LabVIEW’s virtual instrument (VI) capturing measurements of real-life components for more realistic results when combined with simulated circuits. (For more details about VSS-LabVIEW co-simulation, please read AWR’s white paper.)
More Challenges To Overcome
There is no doubt that today’s EDA software tools are more powerful and provide engineers greater design capabilities than ever before. However, technology is constantly evolving and provides a rapidly moving target for EDA software developers. Despite all of the new and improved features, today’s engineers no doubt have a long list of design challenges that EDA tools still can’t solve, along with a wish list of features they desire for their software suite.
What EDA software do you currently use — or wish you had? Why? What types of designs do you currently use EDA software for? What features are most helpful and why? What capabilities do you still need desperately? I’d like to know. Please share your experiences and opinions in the comments section below.