Revolutionizing Electronic Device Manufacturing With Self-Assembling Electronics

By John Oncea, Editor
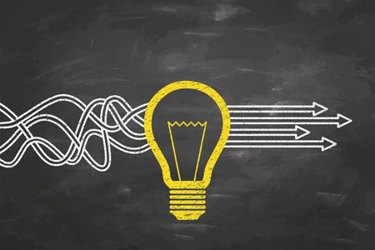
Recent advancements in self-assembling electronics have demonstrated the potential to revolutionize the manufacturing of electronic devices by reducing energy consumption and material waste.
North Carolina State University researchers have developed a novel technique that enables the self-assembly of electronic components, including transistors and diodes, at the nanoscale, writes NC State News. This method involves the spontaneous organization of molecules into structured, functional materials without external guidance, paving the way for the creation of more complex devices such as three-dimensional computer chips.
The National Science Foundation notes this technique proved effective in recent tests and could lead to more efficient manufacturing processes with less energy and waste. IEEE Spectrum adds the successful self-assembly of nanoscale transistors and diodes could significantly impact the future of electronics manufacturing.
These advancements suggest a shift toward more sustainable and efficient production methods in the electronics industry, leveraging the principles of self-assembly to create complex, functional devices with reduced environmental impact.
What Are Self-Assembling Electronics
Self-assembly for electronics involves the autonomous organization of components into structured electronic devices without direct human intervention, according to Cambridge University Press. This process harnesses natural interactions – such as chemical bonds, surface energies, and external stimuli – to form complex systems, often at the nanoscale.
It features spontaneous organization with the components naturally arranged into predefined patterns based on intrinsic properties and bottom-up fabrication which contrasts with traditional top-down methods by starting from individual components (e.g., molecules or nanoparticles) that assemble into the final structure. Self-assembly for electronics also allows for high precision at small scales by enabling the creation of nanoscale features that are challenging to achieve with conventional techniques.
Chemical bonds, surface interactions, and external stimuli like temperature, light, or electric fields all serve as mechanisms of self-assembly which can be applied in several ways, including:
- Nanoelectronics: Self-assembled molecules form transistors and diodes, and nanowires create nanoscale circuits.
- Flexible and wearable electronics: Materials self-assemble into stretchable circuits for sensors and displays.
- Photonic devices: Self-assembled structures manipulate light for optical computing and communication.
- Memory storage: Self-organized materials are used for high-density data storage.
- Sensors: Self-assembled films enhance sensitivity in chemical or biological sensors.
Self-assembly brings with it advantages such as scalability in the form of mass production with lower costs, efficiency via the reduction of material waste compared to traditional manufacturing, miniaturization, and adaptability.
On the other hand, there are several challenges resulting from self-assembly including the need to ensure consistent and defect-free assembly, integrating self-assembled components with traditional electronics, and limited control over very intricate or large-scale systems.
The advancements in self-assembling electronics, as demonstrated by recent research, highlight the potential for more efficient and scalable manufacturing processes in the electronics industry.
NC State’s Ground-Breaking Discovery
As touched on earlier, researchers at North Carolina State have demonstrated a groundbreaking technique for self-assembling electronic devices, potentially revolutionizing the manufacturing of computer chips and other electronics. This method, directed metal-ligand (D-Met) reaction, offers a faster, cheaper, and more efficient alternative to traditional chip manufacturing processes.
The technique involves using liquid metal particles, specifically an alloy of indium, bismuth, and tin called Field’s metal. These particles are placed next to a mold, and a solution containing carbon and oxygen ligands is poured over them. The ligands harvest ions from the liquid metal surface, holding them in specific geometric patterns. As the solution flows into the mold, it forms intricate 3D structures or arrays, which are then heated to create new structures consisting of mixed-metal oxides and carbon atoms.
Key advantages of this self-assembling approach include:
- Speed and cost-effectiveness: The process is significantly faster and less expensive than current manufacturing techniques.
- Tunability: Researchers can adjust the bandgap for semiconductor materials and make them responsive to light, enabling the creation of optoelectronic devices.
- High yield: The method produces more consistent arrays with less waste compared to traditional manufacturing techniques.
The proof-of-concept work has successfully created diodes and transistors, with the ability to fabricate wires ranging from 1,000 nm down to 44 nm in size. While this is not yet as small as the 3 nm features achieved by state-of-the-art manufacturers like TSMC, it represents a significant step forward in self-assembling electronics.
Future applications of this technology could include the creation of more complex devices, such as three-dimensional chips. The scalability of the D-Met technique is limited only by the size of the mold used, opening up possibilities for large-scale production.
As research continues, this self-assembling approach to electronics manufacturing has the potential to transform the industry, offering a more efficient and cost-effective alternative to current production methods.