Microwave-Assisted Heating For The Chemical Industry — And Barriers In Its Implementation
By Dr. Marilena Radoiu, Microwave Technologies Consulting
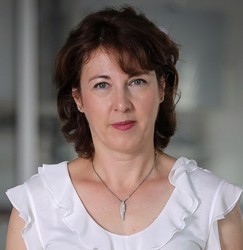
Many technologies are facing challenges in their transition to sustainability; in addition to the performance and quality requirements for current and future materials and processing methods, the industry is also considering the health, safety and environmental risks surrounding these processes. In terms of the environment, the industry and especially the chemical industry contributes to pollution, climate change, biodiversity loss and resource scarcity. Thus, the design of new technologies and new products must be based on an eco-design approach, aimed at considering environmental issues and providing relevant solutions from the product design stage as to implement better practices during the various manufacturing stages. As an important contribution to a sustainable future, the chemical industry and its products must be adapted to a circular economy —a system aimed at eliminating waste, circulating and recycling products, and saving resources and the environment [1, 2]. The form and direction of the technological development must consider that most production stages are critically dependent on the transfer of energy in the process to provide the highest levels of performance and reliability of the final product.
How Microwaves Can Replace Conventional Energy Transfer
The energy provided by industrial, scientific, and medical (ISM)[i] microwaves (MW) is an alternative energy that can replace conventional energy transfer by heat via conduction or convection in industrial-scale processing. Microwave heating is based on the ability of certain materials (liquids or solids) to transform electromagnetic energy into heat. In the context outlined above, this mode of in situ energy conversion directly within materials sensitive to these waves is of great interest for application in liquid, solid, or gas phase materials processing. In addition, microwave heating uses an electric network as the energy source. The use of this energy source with a zero-carbon potential will increase in the future as fossil fuels become scarce and expensive, and their use implies the emission of carbon dioxide.
In microwave heating, the parameters to be considered are related to i) the sample, e.g., volume/mass to be treated, starting products, intermediates and end products, examination of the dielectric parameters of the reaction medium and their temperature dependence, boiling point, viscosity, penetration depth, temperature distribution within the sample and ii) to the equipment, e.g., microwave frequency, microwave energy transfer system, power rating of any microwave component used in the equipment, selection of the reactor (volume, shape and material of construction), which must be both suitable for the treatment with microwave and for the desired process. To these parameters one should also add the value of the electric field inside the reactor, the type of microwave generator (pulsed/CW), microwave power generated, microwave power absorbed, single or multi-mode microwave applicator, temperature control, duration of the operation.
Tests on the influence of microwave in a process can only be meaningful if the R&D study takes into account, or tries to take into account, all or at least a maximum of the parameters listed above.
The number of laboratories around the world investigating the potential of using microwave heating for chemical applications is increasing. Although research and some industrial applications have proved that the implantation of microwave-assisted processing can open opportunities to develop new products and more energy efficient and rapid processes with high potential for the industry, e.g., quality enhancement, better process control, higher yields, smaller footprint, more respectful to the environment, when scaling-up microwave-assisted processes, economic considerations (especially CAPEX) usually eliminate commodity products, and the most successful candidates come from those with high-added value or if the product cannot be produced by any means other than with microwave.
Why Microwave Heating Hasn't Been Fully Adopted By The Chemical Industry
Despite the high number of research publications and reported positive effects, e.g. faster kinetics, improved yield and purity, greener synthesis, the chemical industry in particular is still far from adopting microwave heating as a new technology. This might be explained considering three different scenarios, namely: a) publications, b) equipment/hardware manufacturers, and c) chemistry researchers and their general understanding of the hardware. These factors are further elaborated below:
The Published Work
Almost 40 years after the first use of microwave ovens for enhancing chemical reactions [3, 4], some progress has been made. However, 90% of the published papers still report work done in a kitchen oven more or less ‘dedicated to chemists,’ which cannot be considered valid for scale-up. Microwave-related research is mainly published in scientific journals reviewed by non-microwave reviewers. Similarly, books on microwave-assisted synthesis are mostly authored by chemists who do not have a full understanding of the microwave hardware and how it works. Consequently, most publications in the field do not seem to focus on the microwave hardware as a discipline by itself.
The Manufacturers Of Laboratory/Industrial Equipment
Most dedicated microwave reactors for chemists are made by equipment manufacturers using ‘cooking with microwaves’ techniques. These are more expensive, equipped with touch screens and user-friendly interfaces allowing for different degrees of sophistication with respect to process control, database capabilities, safety features, different vessel designs. However, with no information on the most important microwave parameters, i.e. the forward and reflected power, and hence the absorbed power vs. time (absorbed energy), power density (kW/g) — microwave are just a heating method for fast reactions/high activation energy.
Most of the dedicated microwave laboratory equipment is built using very high-power magnetrons, and researchers use this equipment for processing very small samples. Sometimes this combination leads to strong microwave power densities and ‘magic’ results, which are not scalable in industrial reactors. As there is no possibility to closely monitor and control the reaction as it proceeds, it is very often proposed to work in a pressurized reactor since the solvents and/or reagents can be heated at temperatures higher than their boiling point.
In addition, most of the dedicated microwave laboratory equipment manufacturers are not the same as industrial equipment manufacturers. This also impedes the scaling-up feasibility. Lastly, due to size and price of equipment, frequency at 2.45 GHz is used for dedicated laboratory equipment while industrial equipment is more likely designed to use 915 MHz.
The Researcher
Due to high prices of dedicated microwave reactors, chemists still prefer the kitchen oven to perform reactions. Too often, the chemist is not interested in what is inside the ‘black box,’ and the most monitored parameter is the temperature and/or perhaps the pressure without associating them with the absorbed power/energy and power density obtained from the EM field.
Knowledgeable reaction scale-up encompasses several aspects of chemistry, chemical engineering, and fluid mechanics. Issues arising from kinetics, thermodynamics, and hydrodynamics affect the selection of the most appropriate reactor, its internal design, and its operating regime. To all these we need to add electromagnetic waves and their propagation, temperature-dependent dielectric properties, microwave power density, arcing etc.
Developing safe, robust, and scalable processes calls for a close collaboration between researchers, equipment manufacturers and end users. However, ground reality and publications reveal that, apart from a few exceptions, both researchers and industrial equipment manufacturers fail to put this principle into practice.
Overcoming Drawbacks, Exploring Opportunities
The number of laboratories around the world investigating the potential of using microwave heating to stimulate chemical reactions is increasing. Following up the research, seeing more and more contributions dedicated to chemistry at scientific manifestations, it results that there is a microwave effect with high potential for the industry. This effect meaning all positive contributions to reaction rate enhancement, better process control, higher yield reaction products, and not at last, the excitement of a new technology, which can change the way the chemistry is done.
The plant is not a laboratory. Once production starts, it is difficult to stop and change one or two parameters to make it work. To assure that strategic goals are achieved, knowledgeable and experienced chemists, chemical engineers, and microwave equipment manufacturers must work closely with end users at the outset of the project to clearly identify the project parameters. The greatest opportunity to impact project costs is at the beginning, during master planning and conceptual development. As the project progresses, this ability diminishes. The consequences of the decisions made in early phases of the project will dictate the viability of the project from a financial perspective and also have long term effects on operations and cost of ownership.
The main drawbacks of the microwave-assisted chemistry are very often published to be related to the equipment cost and the low penetration depth of microwave (mainly 2.45 GHz) in the reaction mixture. However, there are ways to overcome these drawbacks:
- Good mechanical stirrers, reactors in series or in parallel, continuous flow reactors, tailoring the microwave chemistry (choice of solvents, catalysts, energy input, etc.). Chemists should know how to deal with these issues.
- Choice of lower frequency (higher penetration depth), higher power density (smaller reactors and potentially lower or no pressure), multiple microwave inlets, synergy with other heating methods, reactors made out of metal (rather than microwave transparent materials), health and safety. Microwave equipment manufacturers should be able to advise on this.
- A higher cost of investment (CAPEX), which should not be looked at as simply as that. The economics are far more complex; the end user will accept a higher CAPEX if the new technology can assure an overall improvement of at least 20% over conventional technology. In addition, if carefully optimized, many microwave assisted synthesis, especially organic synthesis, offer advantages like reduction in catalyst quantity and reduction/elimination of solvents, which render such processes more environment-friendly and can justify higher CAPEX.
- For quicker success, the researcher must work closely with potential end users. They should address together ways to solve existent problems (e.g., treatment and disposal of chemical waste) or to develop new products, perhaps more in the area of specialty chemicals with high added value.
- Probability of successful applications can be increased if microwave are used in combination with other forms of energy/processing, e.g., combination with steam, hot air convection, IR, ultrasounds, etc.
Lastly, the integration of microwave chemistry as a field of study in academic curricula may find today enough justification not only because it is a part of industrial reality but also because of its research and educational potential.
References:
- European Commission, Implementation of the Circular Economy Action Plan (2019), https://ec.europa.eu/environment/international_issues/circular_economy_global_en.htm (accessed on 5th October 2021)
- Kümmerer, K.; Clark, J. H. ; Zuin, V. G. Rethinking chemistry for a circular economy. Science 2020, 367, 369-370, DOI: 10.1126/science.aba4979
- Wan, J.K.S.; Wolf, K.; Heyding, R.D. Some Chemical Aspects of the Microwave Assisted Catalytic Hydro-Cracking Processes. Stud. Surf. Sci. Catal. 1984, 19, 561-568, DOI: 10.1016/S0167-2991(09)60141-5
- Gedye, R.; Smith, F.; Westaway, K.; Ali, H.; Baldisera, L.; Laberge, L.; Rousell, J. The use of microwave ovens for rapid organic synthesis, Tetrahedron Lett. 1986, 27, 279-282, DOI: 10.1016/S0040-4039(00)83996-9
[i] The industrial, scientific, and medical electromagnetic wave band (ISM band) refers to a group of frequency bands or parts of the electromagnetic (EM) spectrum that are internationally reserved for the use of electromagnetic energy intended for scientific, medical and industrial applications rather than for communications. ISM bands are generally open frequency bands, which vary according to different world regions and permits.
[ii] More detailed articles on the subject can be found in:
M. Radoiu, A. Mello, Technical Advances, Barriers, and Solutions in Microwave-Assisted Technology for Industrial Processing, Chemical Engineering Research and Design, 2022, 181, 331-342, DOI: 10.1016/j.cherd.2022.03.029
M. Radoiu. Freins et leviers de l’intégration des technologies micro-ondes dans les procédés de synthèse chimique à l’échelle industrielle. Annales des Mines, Les ondes non ionisantes électromagnétiques et acoustiques : nouveaux savoirs, nouveaux enjeux, 2021, 103, 53-56.
About The Author
Dr. Marilena Radoiu, chartered chemist of the Royal Society of Chemistry (CChem), is the founder of Microwave Technologies Consulting and has worked internationally for more than 20 years in the development of microwave-assisted technologies with applications to chemical synthesis, biomass extraction, plasma, food, etc. Her work has included the engineering and development of novel industrial and scientific standards, custom products, and laboratory equipment. She is author or co-author of more than 50 publications in peer-reviewed journals. She received the Rustum Roy Award (2016), AMPERE Medal (2019), and the award Femme de R&D of the Trophees des Femmes de l’Industrie (2019).
Dr. Radoiu is also a fellow member of several professional associations, including the Association for Microwave Power, Education, and Research in Europe (AMPERE). Dr. Radoiu graduated with a master’s degree in technological organic chemistry from the Polytechnic University of Bucharest in 1993 and received a Ph.D. in radiochemistry and nuclear chemistry in 1998 from the same university in collaboration with the Institute of Atomic Physics, Bucharest. She received an executive master’s degree in business administration (MBA) from the Ecole de Management Lyon (EM Lyon) France in 2018.