How The Fabless Business Model Can Drive innovation, Capacity To RF Filter Industry
By Robert Hammond, Resonant
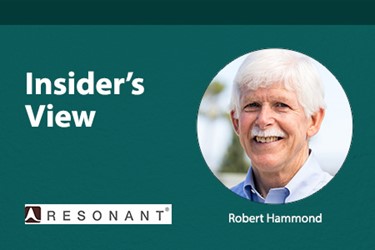
It’s not much of an overstatement to say that, without significant innovation and new entrants to the market, the RF filter is quickly becoming the bottleneck to emerging 5G services, autonomous cars, IoT, and wireless medical applications.
The market for filters — estimated by analysts at Yolé Développement at 30 billion devices in 2016 — is growing at greater than 20 percent per year, driven by innovative new wireless applications, as well as the need for more filters in next-generation mobile devices. It is estimated that today’s 4G phone requires 60 filters, whereas 5G phones will require more than 100 filters.
But, it could be tough to meet these growth targets, as RF filters are still empirically and painstakingly developed. This is decades after the semiconductor industry started utilizing a combination of electronic design automation (EDA) tools and standard IP libraries to usher in an age of fabless semiconductor manufacturers — unleashing tremendous innovation.
What the RF filter industry needs is more fabless filter manufacturers, and the infrastructure is now in place for these firms to emerge.
RF filters, for the most part, require multiple fab cycles to optimize the performance of each device. Using a design process called the acoustic wave ladder, RF engineers start their designs with a similar, known design. This gets them in the ballpark, but then they need to construct a prototype filter, test it, and then make changes to optimize performance empirically.
This can go on for a dozen or more iterations before the filter’s signal properties are optimized to meet the specifications. This design process can take months or years — and that’s for standard RF filters and duplexers. Now, there is increasing demand for multiplexers for carrier aggregation, as well as for very complex bands (like band 41) that are being utilized in China and other markets for high-bandwidth services.
Because of the complexity of this process, an estimated 80 percent of the RF filter market comes from four vertically integrated filter manufacturers. Merger and acquisition activity in the industry is heating up because of the projected market growth, but also due to the strategic nature of filters to mobile devices.
When Qualcomm acquired 51 percent of its RF filter joint venture with TDK, it took control of a business that produces 25 million filters per day. Some companies who compete with Qualcomm were left scrambling for a new filter source because their competitive differences left them not able to buy from Qualcomm. These conflicts will increase as other vertically integrated filter manufacturers become acquired.
Carrier Aggregation Driving Increased Filter Complexity
Carrier aggregation and other industry developments mean the complexity of RF filters will lead to longer development cycles. It is estimated that carrier aggregation could be needed in more than 25 billion RF paths by the year 2022, and every RF path needs one of these very complex filters. Carrier aggregation is facilitating the higher data rates that consumers want and applications require, but at a cost of significantly more complex RF front ends (RFFE).
Fabless Filter Vendor Challenges
Adopting a fabless business model is not without challenges. Companies who are used to purchasing parts from other vendors must shift from a procurement mindset to a product development mindset — even if they are able to outsource the work. Some of the processes that need to be managed by the fabless filter companies include:
- Making sure the fab has the capabilities needed to support your business model — Some module makers want to integrate the filter into their RFFE module. This means sourcing wafer-level packaging for their filters to maximize the space in the module. A company selling a standalone product may want a surface mount package (SMP) option. Asking these questions is a critical first step for fabless filter manufacturers.
- Managing reliability testing — Reliability testing includes testing the part at power levels representing the high end of its power range to ensure functionality under adverse conditions. Durability testing, where parts are high-power tested at temperatures representing the high end of their operating range, for long durations, also is critical. Fabless filter firms must negotiate with the vendor for this testing, or set up their own testing facilities.
- Negotiating die yield and who pays for defective parts — The fabless filter maker will contract for a certain die yield, but then must test each die to isolate defective chips and ensure these bad filters are not packaged. Working with the fab to minimize defective parts is an internal process critical to the profitability of an RF filter business.
All of these issues add complexity to the decision to become a fabless filter manufacturer. While some of these functions can be outsourced, the fabless filter manufacturer must be ready to be much more involved in the product design function by taking what had been a procurement function and making it into a product marketing and support function.
Can The RF Filter Industry Support A Fabless Model?
Shifting from a procurement mindset to a manufacturing mindset will help overcome many of the challenges listed above, but several other macro factors are needed before the industry moves in this direction:
- More suppliers recognizing the opportunity — Many companies exist that could participate in the RF filter market, including module manufacturers, RF passive manufacturers, foundry and packaging firms, or even mobile device OEMs or carriers. Currently, all of them participate in the market in some way, and could add filter capacity (or consume filters, in the case of OEMs). For many companies, adding a filter product line is a natural fit with their current business, but they simply are not aware of the opportunity, which makes it a market education challenge to increase awareness.
- Design Automation — One of the biggest drawbacks to innovation is the drawn-out and iterative manual product development process. With automated design tools and services, less time and resources are required for product development, and products get to market more quickly. This development was key to the fabless model for semiconductors, and it is essential for RF filters to follow that trend.
- Foundries /Back End Services — While vertically integrated filter manufacturers have their own fab facilities, there also are non-captive fabs that can manufacture filters. Similarly, firms that will package the die into usable devices are plentiful. In both cases, evaluating these services’ capabilities for volume, quality, and cost become the key factors. In short, new fabless players could build their own ecosystem of partners needed to enter the market, or they could participate in specialized ecosystems set up by vendors.
Already, a number of companies are pursuing this path, which bodes well for unleashing the creativity needed to keep ahead of the market and ahead of the needs of new services. Following the lead of the semiconductor industry shows us a path forward by adopting a fabless model where specialist firms split up the product development and business functions required to bring a product to market.
[Editor’s Note: Resonant has established the ISN Foundry Program, which assists companies in developing a fabless RF filter business. Click the link above to learn more]
About The Author
Dr. Robert B. Hammond has served as Resonant’s chief technology officer since June 2013. Prior to founding Resonant, Dr. Hammond served for more than 20 years as Senior VP and CTO of Superconductor Technologies, Inc., where he was involved in the development of high temperature superconducting materials, cryogenic refrigeration and packaging, and RF and microwave circuits. Prior to that, he was leader of Electronics Advanced Development at Los Alamos National Labs. Dr. Hammond holds a BS degree in Physics, an MS degree in Applied Physics, and a PhD in Applied Physics, each from the California Institute of Technology.