Predicting Product Quality At TEN TECH AERO
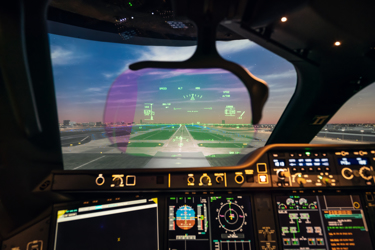
About the Customer
TEN TECH AEROSPACE & DEFENSE, INC. provides multi-discipline engineering services including high-end mechanical engineering design, analysis, physical testing support and hardware prototyping services. Because their customer list includes, but is not limited to, large defense contractors, accuracy and speed to result are top priorities.
With decades of industrial experience and high expertise in computer-aided engineering (CAE) tools and methods, TEN TECH AERO is able to predict product performance without the use of costly physical prototypes.
TEN TECH AERO pride themselves on being the most responsive, cost-effective and highest quality partner in the market. “Speed, quality, and quantity do not have to be mutually exclusive,” says Managing Director, William Villers.
Their Challenge
Because speed and accuracy are top priorities for TEN TECH AERO, they are constantly evaluating their tools to ensure they can provide the type of service that they are known for. At one point, they were seeing consistent crashing and long processing times from their previous tool, to the extent that processing could take up to two weeks. These were classified as “known bugs,” so rather than receiving support for these challenges the recommendation was to recreate the models. Since they historically have worked with large designs, where more than 200 million elements are common, they knew they needed a better solution for every step of their CAE process from preprocessing, solving and postprocessing.
TEN TECH AERO also needed a tool that could work with their existing legacy data, as they could not afford to lose many years’ worth of models the teams had created and stored. Processing time was a big issue for them as well. One of TEN TECH AERO’s key differentiators is that they do not charge their customers for solving and processing time. This means that extra time spent on processing is time that isn’t spent on billable services. With their previous tools, at times processing could take up to a full day.
Get unlimited access to:
Enter your credentials below to log in. Not yet a member of RF Globalnet? Subscribe today.